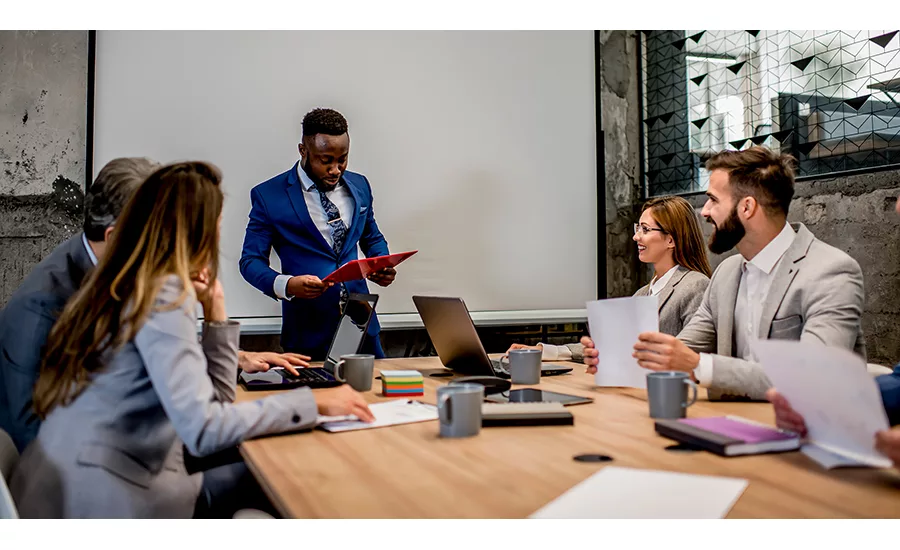
Photo courtesy of Getty Images / Dmphotol
Building an Automation Infrastructure
Unless you operate a brand-new state-of-the-art plant, you probably have a facility with a mish-mash of aging processing and packaging equipment with various vintages of network and application software support—maybe several areas requiring manual labor. But even a brand-new plant today is tomorrow’s aging facility, eventually needing equipment and software updates to keep it running with minimal downtime, peak efficiency and consistent product quality.
For older facilities, knowing where and what to automate—what your priorities should be—is important to helping you stay competitive now and in the future. For those with new plants, it’s never too late to plan your future goals. In this article, we consider how to know when, where and what to automate in an older facility. Of course, the answers to these questions won’t be the same for every plant.
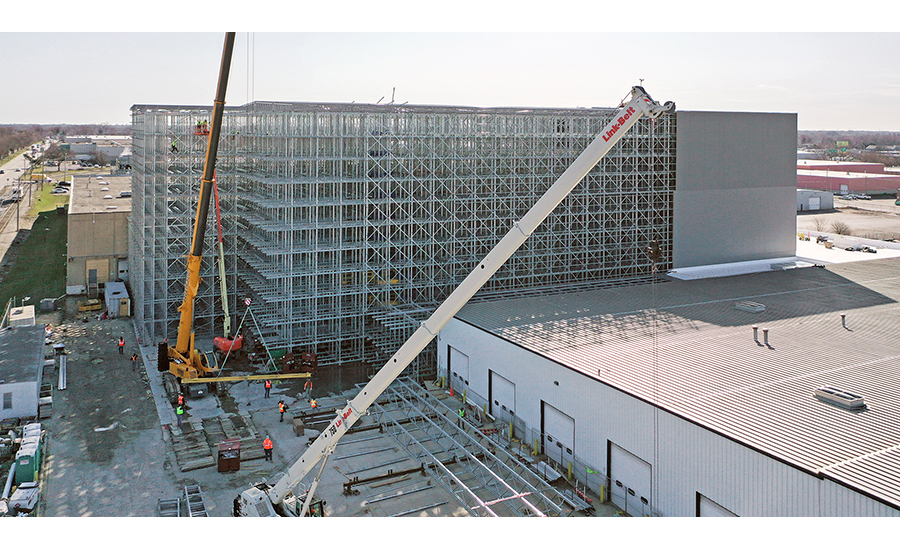
Automation Solving Labor Shortage Problems
The primary motivations driving food processors to automate their operations include labor reduction, increased production efficiency and enhanced product quality, says Ryan Beesley, CAP, regional engineering manager – Kennewick, Concept Systems, Inc., a Control System Integrators Association (CSIA) Certified Member. But the labor aspect has especially been an acute problem for the last couple of years.
“The COVID-19 pandemic has highlighted labor-related challenges in the industry that weren’t totally apparent before,” says Beesley. “In response to the pandemic, food processors had to ensure that the population had a consistent supply of products while coping with an unstable labor market that could impact their workforce in significant numbers. Since food production was classified as an essential service, meeting the demand became a top priority. The pandemic also exposed vulnerabilities in existing processes as they were pushed beyond their capacity limits. The shortage of labor had a more profound impact on the production systems than anticipated, leading many producers to adopt automation solutions rapidly.”
Additional production lines can increase output, but labor remains an important consideration in any project. “We had a food manufacturer that needed significant additional capacity, driving a need for design and installation of additional production lines,” says Alfredo Valadez, Burns & McDonnell project manager for global facilities. Those lines were designed with the latest automated technology that reduced manpower and increased quality and separately added protection from operational disruptions due to labor shortages. With fewer people required to operate the production lines, the risk of people not showing up and causing disruption to production was reduced.
According to David Campbell, Burns & McDonnell department manager for global facilities, in the facility Valadez just described, while the addition of new production lines increased capacity by 60%, a fully automated 40,000 pallet position warehouse was added to augment capacity. Automating the warehouse resulted in a 50% reduction in cost per case though consolidation of storage onsite. The automation component has also driven a 40% reduction in labor cost per case and 50% reduction in maintenance due to retiring obsolete automation processes.
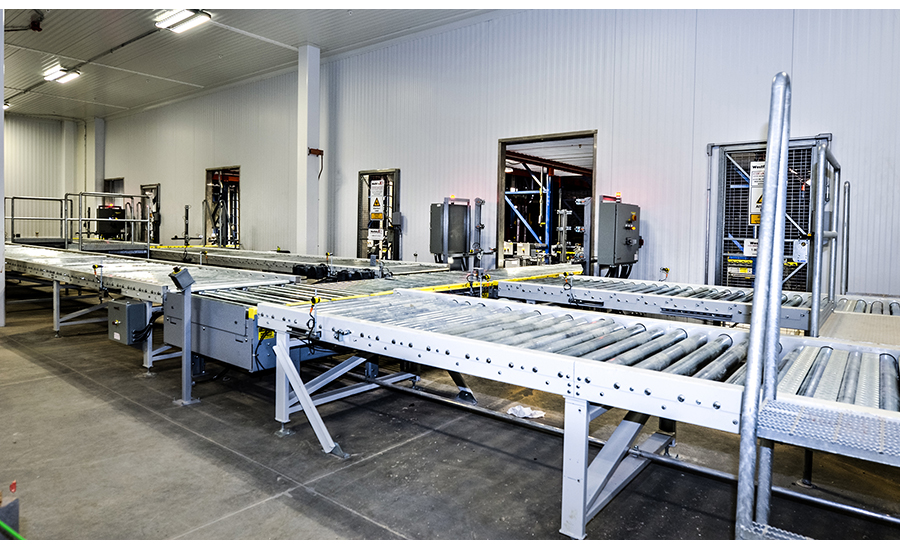
The warehouse has always been a labor-intensive area with distribution costs rising and jobs getting harder to fulfill, plus people are not as willing to work in cold environments, adds Mark Livesay, ESI Group VP automated warehousing. Higher demand for products means an increase in production capacity, which then drives warehouse growth. With site restrictions and land becoming more expensive—and to relocate a production facility to another location is not often feasible—it makes sense to go vertical via an AS/RS facility. Automation is becoming more and more necessary to get the product to the dock for transport to the consumer. Product shrinkage is all but eliminated with AS/RS automation since the inventory is 100% accurate and traceable.
Other Roles for Automation
Quality—Why not use automation to enhance quality, meaning less waste and fewer scraps? For example, a large confectionery manufacturer faced a problem with quality deviation incidents, according to Pete Gabor, director of business development, Glassdome, a CSIA Member. Over the last five years, the number of SKUs had more than doubled. The introduction of new raw materials, equipment and procedures resulted in more than doubling of the number of quality deviation cases. One of its major lines’ size, thickness and flavor quality tests were performed manually and were labor consuming. At regular intervals, samples would be taken from the line, measured, handwritten into a journal entry and then entered into their quality management system, says Gabor.
“To automate this process, we deployed a vision system connected to our Glassdome IoT gateway on the line,” adds Gabor. “The system measured the size and thickness of every product and recorded the results automatically. We loaded all historical process data and correlated it with sensory quality inspection reports to address taste quality deviations. To find the optimal parameters, correlations between ambient temperature, humidity, formulation temperature, oven humidity, marshmallow consistency, size and chocolate temperature were examined. This approach detected and displayed quality violations in real time, but we also needed to predict when upsets would occur.
“To address this issue, we created a data model that includes real-time anomaly detection and forecasting,” says Gabor. “We were able to identify problems such as oven zone abnormalities and provide an early warning system when plant conditions needed to be modified to preserve quality consistency.”
This solution reduced personnel and quality deviations, and allowed for more units to be manufactured. The candymaker was able to redeploy the manual test personnel to other areas of the factory while reducing the size standard deviation by 69% and the thickness standard deviation by 64%, reports Gabor.
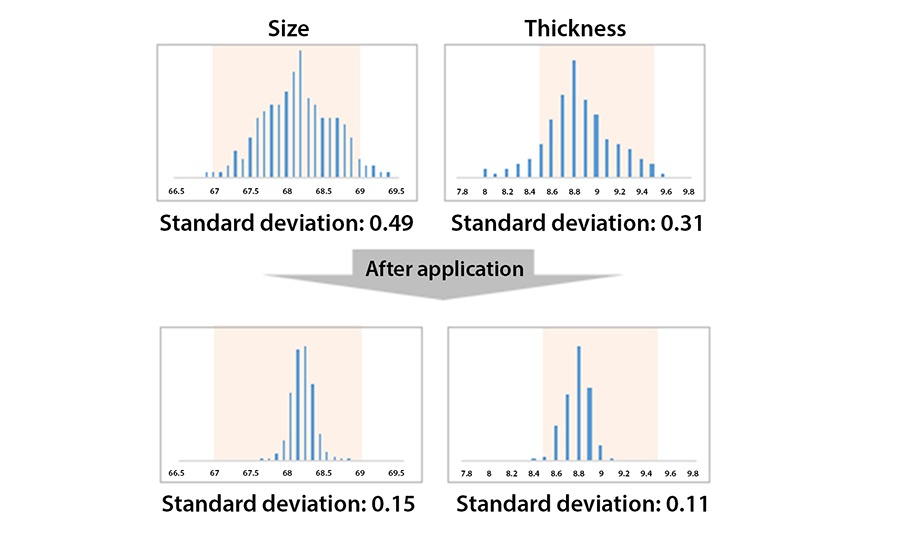
Downtime reduction—You know, the big losses that occur with just a little downtime. Rao Kolla, PE, CSCP, MBA and Stellar director of process electrical/controls engineering, reports having worked with a Fortune 500 food manufacturer that had a facility struggling with significant downtime on its packaging equipment. “We installed downtime software for one of the packaging lines and advised the plant manager to form a cross-functional team that could confirm the challenges and proposed solutions.
“It took time for adequate data collection to validate the accuracy on that packaging line, but once that was established, the plant manager immediately called me back, asking when we could do the same on more of their lines,” says Kolla. “This automation led to a 5% reduction in overall downtime, which ultimately translated to a 60% improvement overall. It was as if they gained an extra packaging line without having to build one.”
Process automation—Dean Elkins, senior director, advanced automation at Gray Solutions, a Gray Company, has automated plants from receipt and delivery of raw materials to manufacturing, packaging and loading of finished goods. “Efficiency gains have been realized through the implementation and monitoring of process controls and manufacturing data, automated in-process testing and inspection procedures and flexible automation that augments manpower while meeting food and industrial safety standards.”
But, if you can’t automate an entire facility, maybe a good place to start is in batching. “Although we have implemented solutions throughout food processing facilities, we have found that our batching solutions have made the most impact for our customers,” says Tim Barthel, vice president – automation solutions at Cybertrol Engineering, a CSIA Certified Member. “By optimizing this process, we have increased throughput, decreased downtime and rework, and improved quality by understanding our customers’ challenges in automating these processes. We also provide value-add solutions, such as integrating and automating our customers’ recipes that are stored in their ERP systems, which historically required clipboards and paper.”
Standardization—While standardization in and of itself may not be a benefit of automation, it is certainly a necessary ingredient in preventing those infamous islands of automation. “Standardization facilitates the integration of different machines, lines and production areas from the plant,” says Enmanuel Aparicio-Velazquez, Siemens AG Digital Industries factory automation technical account management. “The benefit: Shop floor connectivity enables data to be converted into production transparency and performance indicators for resources optimization.”
This standardization needs to be an inherent part of automation hardware and software technology; define data communications protocols for the shop floor (e.g., OMAC, MTP) and link standardized solutions together—such as SCADA, KPI monitoring, operations management, predictive maintenance, etc.
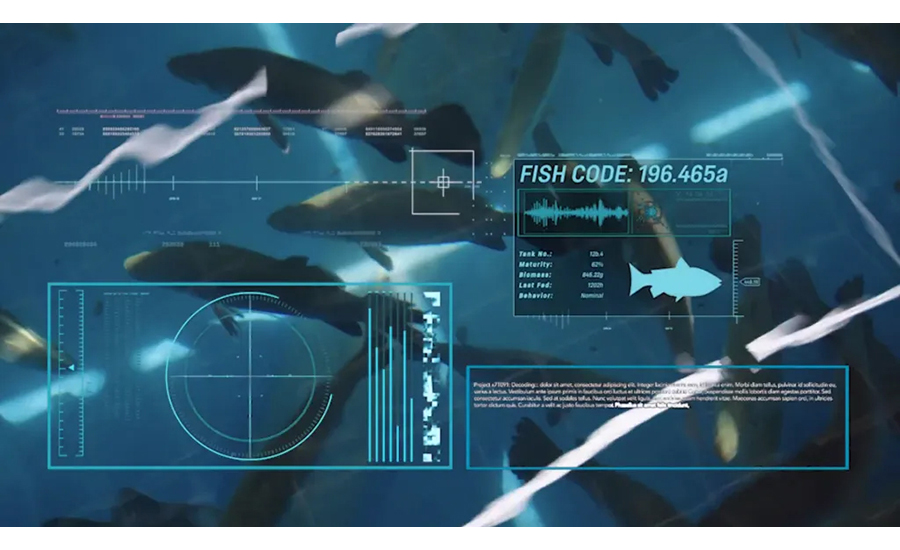
Getting Started in the Planning Process
No two automation solutions will be the same—everyone is unique. “Custom automation solutions typically begin with a feasibility and concepting phase that involves a deep dive analysis of existing operations and data,” says Burns & McDonnell’s Campbell. “Following this, a detailed design and a firm cost estimate are provided. Finally, the onsite execution phase typically includes engineering oversight, construction and systems installation and startup services.”
“E Tech specializes in Front-End Engineering and Design (FEED) studies that help our clients approach their control systems strategically,” says Cassy Gardner, director of operations, Vacaville, Life Science, E Tech Group. “We have a proven process we bring to our clients to help them solve unwieldy, open-ended problems.
“What is most critical to success in our experience,” says Gardner, “is that needs and outcomes for all stakeholders are well-defined at the outset. Doing so systematically can unify stakeholders and reduce costly late-stage changes.”
“At the onset of the assessment, we gain an understanding of where the executive team perceives deficiencies in their current systems, which provides us with an overview to narrow our focus,” says Concept Systems’ Beesley. “Then, we interview production managers, production leads and operators to identify areas of concern. Typically, production leads and operators possess a wealth of knowledge on their processes and can easily direct us toward problematic areas. We observe how they operate their equipment and seek ways to enhance their job efficiency and ease of use. Our aim is not to eliminate operators but to equip them with the necessary tools to be more effective in their job processes. For example, this can range from providing them with more actionable data on an HMI to automating a physically or mentally taxing process entirely.”
Next, Concept Systems prioritizes processes that are highly repetitive, require minimal internal training or involve operations that are complex but are typically performed by operators that closely mimic automated operation.
After the assessment, the system integrator (SI) meets with stakeholders to select projects that provide the best ROI. These may range from data acquisition improvements (which is used to determine the areas needing modernization) to machine control retrofits or multi-year upgrades. The process uses assessment insights to prioritize projects that align with the organization’s strategic goals and delivers tangible benefits.
What Areas are Easier to Automate?
Maybe a better question should be based on value, says Siemens’ Aparicio-Velazquez. “The decision to automate manufacturing areas should be focused on value rather than easiness or difficulty of implementation. Quick wins are OK. However, they must be obtained as the result of actions executed after exploring, identifying, deciding and analyzing the business drivers, considering all company stakeholders.”
Processing or pre-packaging is typically the easiest to automate, due to less complexity when handling the product prior to packaging, says Valadez. Packaging requirements can create varying complexity in designing automation. Some packaging is designed for automation, making automation easier, while other packaging is designed for ease of use. For example, retail-ready cases are sometimes not the easiest to automate due to the case and product orientation. These packaging designs are intended to make it easy for retail presentation and consumer attraction, but not necessarily for automation equipment.
Processing and production tasks can be prime targets for automation because these tasks usually have high levels of repeatability and consistency, says Campbell. Additional areas in the plant where there are bottlenecks to production are ripe for automation. These areas typically soak up a large amount of labor expense—or there are large volumes of buffered material that are staged and awaiting processing, or manual processes are leading to high rates of quality defects. Automating these areas can provide substantial returns on investment.
“Ease of automation and ease of justifying it to the end user are both parts of this question that need to be considered,” says Cybertrol’s Barthel. “It is easy to add automation into the cleaning and process systems in a facility, but only if the end user is willing to add the necessary instrumentation to allow for automated control. For example, we have some tried-and-true improvements around CIP systems that would not take a lot of effort to implement, but getting the end user to add instrumentation to allow this type of improvement can be the initial hurdle.”
If a processor is looking to improve safety and efficiency, automating material handling may be a great place to start, says Paige Minier, manager, OT infrastructure at Gray Solutions. There will be fewer forklifts maneuvering around the plant, fewer workplace injuries from manually moving material and improved efficiency by moving material through conveyors, robots and other automated systems.
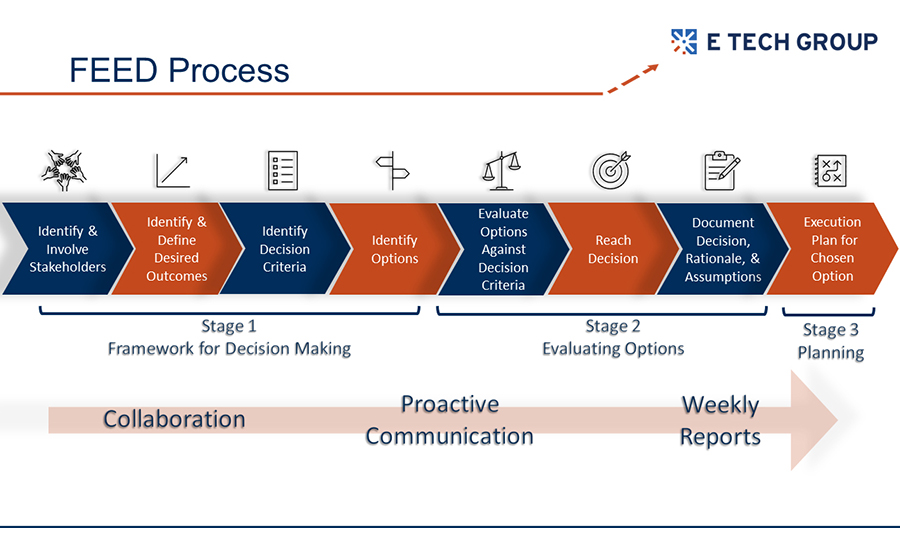
What Areas are Tougher to Automate?
“Areas with a high level of work variability, a high level of manual tasks and a high number of unique items in the same area are the most difficult to automate,” says Glassdome’s Gabor. “Automation engineers must be pessimistic when developing an automation solution. We must consider every possible negative scenario and devise a solution to avoid it. The solution becomes increasingly difficult as the variability grows.”
“It’s difficult to point to a specific area of difficulty for the whole industry,” says Valadez. “It is dependent on the product and process. For example, it can be problematic and expensive to automate packaging if it is not designed for automation. Also, low-volume/high-mix processes are difficult to automate, as they require significant flexibility in the system. This translates to an expensive system that has low ROI due to the low economies of scale.”
Operations that have a lot of variability in either production requirements, materials handling or miscellaneous tasks to be performed can be difficult to automate, adds Campbell.
“It can be difficult to automate areas of the plant that see little product uniformity,” says Gray’s Elkins. Devices like fixtures, robots and packaging machinery are designed to function with an expected part presentation. While non-uniformity can often be solved through the addition of sensors, including machine vision systems, this could add complexity and cost to the solution. Another consideration is the suitability of the automation equipment to the environment. Special care must be taken in cold or washdown areas or in equipment that requires food-grade grease, for example.
Not all areas lend themselves to inexpensive solutions—for example, labor-intensive areas such as product handling, packaging and then warehousing (storage and order picking), says ESI Group’s Livesay. There are some areas that are very expensive to automate and do not have a good ROI, e.g., piece picking. It is easy to ship out full pallets, and one can justify layer picking scenarios, but at some point, a decision must be made if they can justify the additional automation expense to get to piece picking levels.
Legacy Systems and Costs
“We have found that upgrade opportunities with legacy systems can be the most difficult sell since these systems are currently running a plant’s operation—and a replacement in some cases is only avoiding future downtime—the costs and definition of a true production ROI become a challenge,” says Cybertrol’s Barthel. It is difficult to sell an upgrade when a processor has an intent to minimize cost without looking at long-term gains that they can benefit from automation. Focusing on cost alone can prevent the manufacturer from implementing a more robust system that is less likely to have downtime due to legacy systems. An unwillingness to add additional instrumentation prevents the collection of very valuable information that is needed to improve production, adds Barthel.
Here’s a related issue. Getting buy-in from the operators on the plant floor can be one of the most significant obstacles to furthering a plant’s automation, says Stellar’s Kolla. Change is inherently difficult for some people, but many often equate “automation” with “I’m being replaced,” though that’s often not the case. Education is critical because the technology is evolving rapidly, and this “fear of the unknown” can significantly hinder a manufacturer’s ability to thrive or, in some cases, survive.
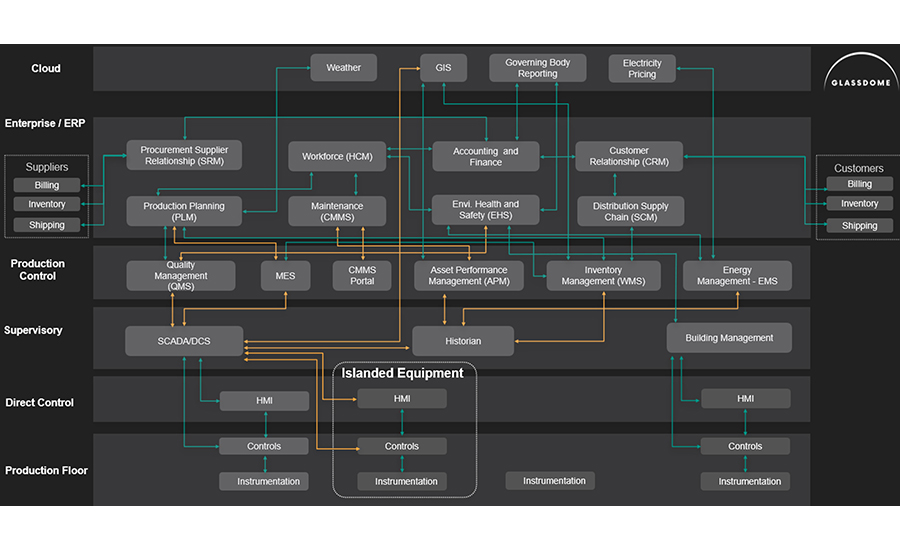
“Gotchas” or the Hidden Issues Thwarting Successful Automation Projects
Finally, if you’re contemplating an automation project, there are always the hidden traps that can quash a successful endeavor. Some of these issues include:
- Lack of electrical services needed to support new equipment. Costs to build out these services can quickly add up if not managed before a project begins.
- Legacy and homegrown systems in both processing and the warehouse can slow a project if they can’t connect data to other systems.
- Lack of established and documented standards, wiring and network diagrams, etc. slows an automation project, especially if those who wrote the documents are no longer employed at the facility.
- SI or engineering house has not been made aware of all—especially legacy—systems at your facility.
- Lack of a best-practice infrastructure for your plant.
- Similar to the first point, lack of infrastructure support for new equipment. Utilities—power, gas, water—and the biggest one is structural. Can the roof support new ceiling loads such as refrigeration equipment, material handling equipment, etc.?
- Some floors may not support AGVs.
- Can the facility safely accommodate new network wiring and equipment and automation machinery?
- Software from different vendors may not communicate with other software and equipment without integration, middleware and custom programming.
- Cybersecurity readiness—or lack thereof.
- Be aware of all the issues before moving software applications to the “cloud.” (See the sidebar, “Considerations to Moving Applications to the Cloud.”)
Automation Today and in the Future
Automation—you can’t live without it and be competitive. “Automation in many cases is viewed as a commodity, when in actuality, once the equipment is put in place and starts depreciating, automation is what drives profitability within a manufacturer’s operation,” says Cybertrol’s Barthel.
“Automation is just as good as how it is integrated into your company’s operations, how eager your culture is to embrace it, and the assumption that it will always evolve,” says Glassdome’s Gabor. “The most successful projects I’ve been a part of embraced those three philosophies. I encourage you to do the same.”
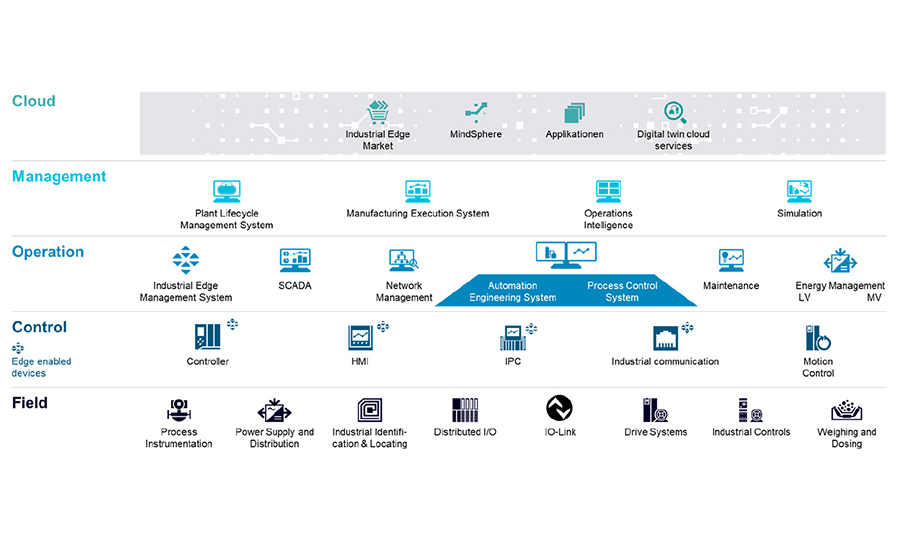
Considerations to Moving Applications to the Cloud
Many vendors are transitioning their offerings to cloud-based services due to significant advancements in the reliability and security of such services. For example, a manufacturer of data recording apparatuses offers a cloud-based solution that meets all food safety and cybersecurity requirements, replacing traditional paper sheet-based data recorders. This is a great alternative for data retention and compliance.
While cloud-based systems can be a smart and cost-effective option for certain food producers, it’s important to undertake a careful and methodical evaluation of the pros and cons before making the switch. Some food processors may find that cloud-based services are suitable for managing most enterprise-level operations, while others may have difficulty moving away from traditional control systems.
When considering transitioning to cloud-based control systems, the safety and reliability of the process must be a top priority. It’s essential to determine whether the process can be controlled safely and reliably without local controls. If the answer cannot be confidently given, and without buy-in from all levels of operations and management, then the process should not be considered a candidate for cloud-based control.
The decision to transition to cloud-based control systems should involve careful consideration of the risks and benefits, as well as a thorough evaluation of the specific needs and requirements of the food processing operation. If cloud-based control systems can provide the necessary level of safety and reliability, then they can offer numerous benefits, such as enhanced accessibility, flexibility, and scalability. However, it’s crucial to ensure that these benefits do not come at the expense of process safety and reliability.
One alternative to fully transitioning to cloud-based control systems is to utilize software services from a company like Rockwell Automation, which offers a range of cloud-based services. For example, their FactoryTalk Design Hub software provides development tools that enable plant personnel to evolve and maintain systems without the need for multiple software revisions and programs.
This approach can provide the benefits of cloud-based services while maintaining some level of traditional control. It allows for more efficient and streamlined development processes, with access to the necessary tools and software available through the cloud. At the same time, it can help ensure the safety and reliability of the process by maintaining local control systems for immediate and critical functions.
— Ryan Beesley, CAP, Regional Engineering Manager – Kennewick, Concept Systems, Inc.